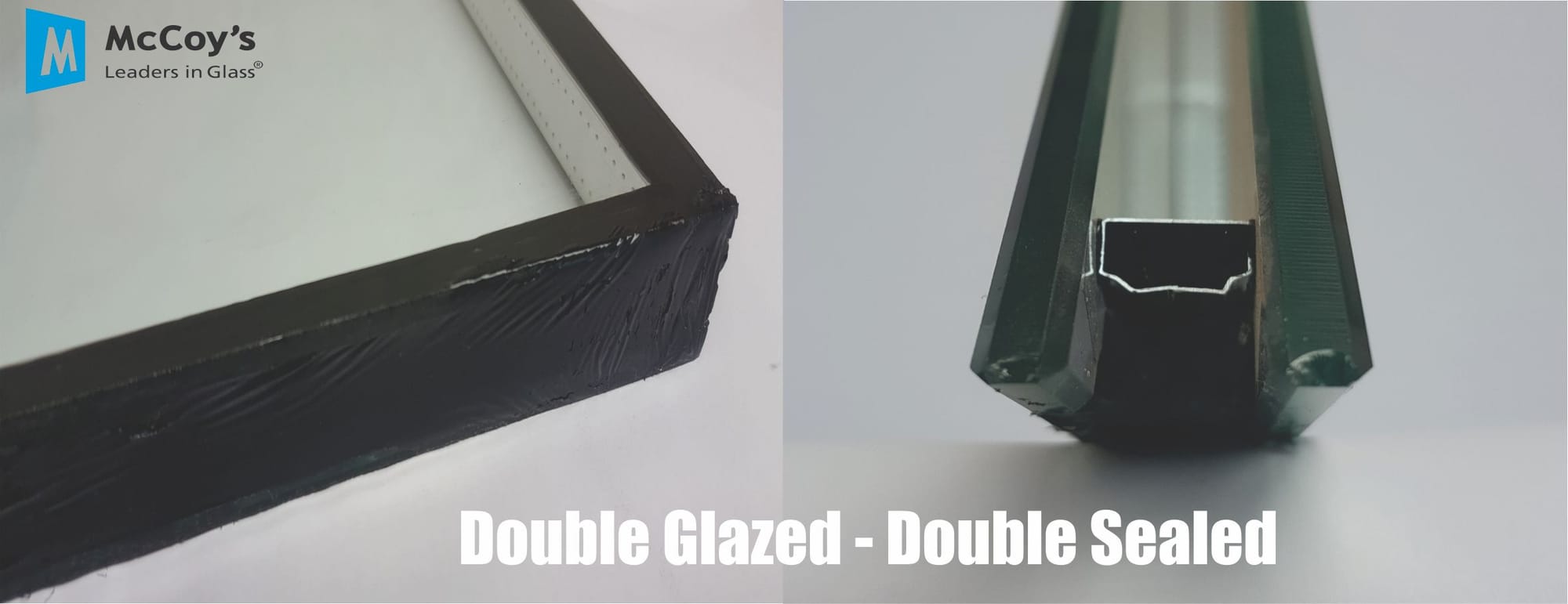
Sealed Insulated Glass Units (SIG’s) are manufactured from two or more panes of glass held apart by a spacer, trapping dehydrated air between the glass panes.
Their primary function is to improve the thermal insulating properties of a glazing product, as well as contribute to safety, security and acoustics.
McCoy's Glass manufactures Double Sealed SIG units.
The appearance and performance of SIG Units can be modified by incorporating different glass types and thicknesses, altering the width of the spacer bar.
Double-glazing
The airtight construction of double glazed windows creates thermal insulation. This reduces the flow of incoming and outgoing heat. Less energy is used to heat up or cool down your home, resulting in lower energy bills. In the process of double-glazing a window is formed from two panes of glass, with the space in between filled with dehydrated air or a gas, making them ideal insulation agents. Having double glazed windows will help keep the heat out in summer, and keep in the warmth in during winter, cutting down on the number of times your heating or cooling system has to switch on and off.
Apart from excellent energy savings, double-glazing offers a host of other benefits:
Double Glazing can reduce the greenhouse gas emissions from your heating and cooling significantly, and reduces your carbon footprint.
Double glazing could seem a bit costly at first but will end up saving you a lot of money by reducing the money you would spend on heating or cooling your home. These aesthetically beautiful windows will also instantly enhance the value of your home.
The benefits and functions of SIG Units include:
- Improved sound reduction
- Improved security
- Improved resistance to wind-loads
- Improved thermal insulation
- Improved solar energy control
- Minimized condensation
Handling & Storage
- Stack on edge in a vertical position at 90° to its base support, with cushioning between floor & edges
- Do not stack more than 6 deep without intermediate support for each stack
- Store in a dry environment away from direct sunlight. Prolonged exposure to dampness may lead to product breakdown
- Do not cover with plastic as condensation may damage edge seals
- Never store or transport horizontally
- Carefully remove all labels after glazing
- Do not damage edges in any way before or during installation. Even minor local shelling may increase the risk of glass breakage
- Never attempt to grind or nip the edges as this can damage the seals & lead to glass breakage
- Damaged SIGU’s must not be glazed
- Protect SIGU’s during construction. Guard against contact with wet cement or other alkaline solutions released during rain from concrete or masonry as this can cause staining
- Protect from hard foreign objects, metals, abrasives, welding & grinding splatter, sandblasting, caustic plaster materials & excessive temperatures
- If glazing in higher or lower altitudes than where SIGU’s are produced consult McCoy’s Glass prior to manufacture as pressure equalisation tubes may be required
Frames
- Frames beads & fixings must be adequate to support & restrain SIGU’s, with stand windloading, SIGU weight & building movement
- Ensure that all framing members are plumb & square
- Width of the frame rebate must be sufficient to accommodate the SIGU thickness, plus face clearance, plus bead
- Never force SIGU into frames
- Ensure glazing rebates & drainage weep holes are free from debris & obstructions
- Glazing surfaces must be free from moisture, oil, dirt, grease & any other contaminant material
- Screws, bolts or other obstructions must not protrude into the glazing channel
Clearances
- SIGU’s must have adequate edge clearance for the full thickness of the unit
- Setting blocks must allow drainage to pass weep holes
- Any point loading must be avoided
- Edge clearance should be not less than 10mm & face clearance not less than 5mm in accordance with SANS 10137:2011
- In bead glazed applications, edge cover should be a minimum of 12mm
Sealing/Drainage
- To ensure good performance at all times, all external junctions of glass & frame must be effectively sealed against penetration of weather
- SIGU’s to be installed so that retention of water in the frame is prevented in the proximity of the edge, as prolonged contact with moisture at the seal of the unit may lead to seal failure
- Ensure rebates are well drained with minimum of 2 weep holes per sill, each 7mm x 3mm at maximum 500mm centres
- Timber or concrete rebates where in contact with glazing compounds must be completely sealed with an appropriate sealer
Setting Blocks
- SIGU’s must be centrally located in the frame with the bottom edge resting on at least 2 full width setting blocks
- Setting blocks must be at least the full width plus 3mm greater than the SIGU thickness
- When pushed hard against the back of the rebate, they must fully support the bottom edge of the SIGU across its full width i.e. supporting both inner & outer panels
- Use minimum 3mm thick for domestic & 6mm for commercial applications non-absorbent, resilient neoprene, santoprene, pre cured silicone (in the case of silicone flush glazing) 50 – 90 Shore A durometer hardness
- Length shall not be less than 30mm per square metre of glass area
- Composition must be compatible with the SIGU edge seal
- With the exception of pivot sashes setting blocks must be placed ¼ of the frame length in from each corner (quarter points) or 150mm from corners, whichever dimension is greater
- For pivot sashes setting blocks must be placed over the pivot point
- Location should be in accordance with SANS 10137:2011
- Edge blocks 50 – 90 Shore A durometer hardness must be used opposite each other on all 4 faces on each side of the SIGU to maintain clearance ad prevent movement under wind pressure. Length shall not be less than 25mm
- Do not attempt to force the edge blocks as this will result in fracture
Thermal Stress
- Always glaze reflective or tinted glass to the outside of a building
- The use of tinted or reflective glass leads to increased absorption of solar radiant heat. This results in higher thermal stress, which may lead to fracture. Where significant risk exists toughened glass may be required
- No plastic film, sign or label or other opaque material or similar device should be applied to any large area on the surface of the glass. These may absorb heat, setting up thermal stress which may lead to cracking
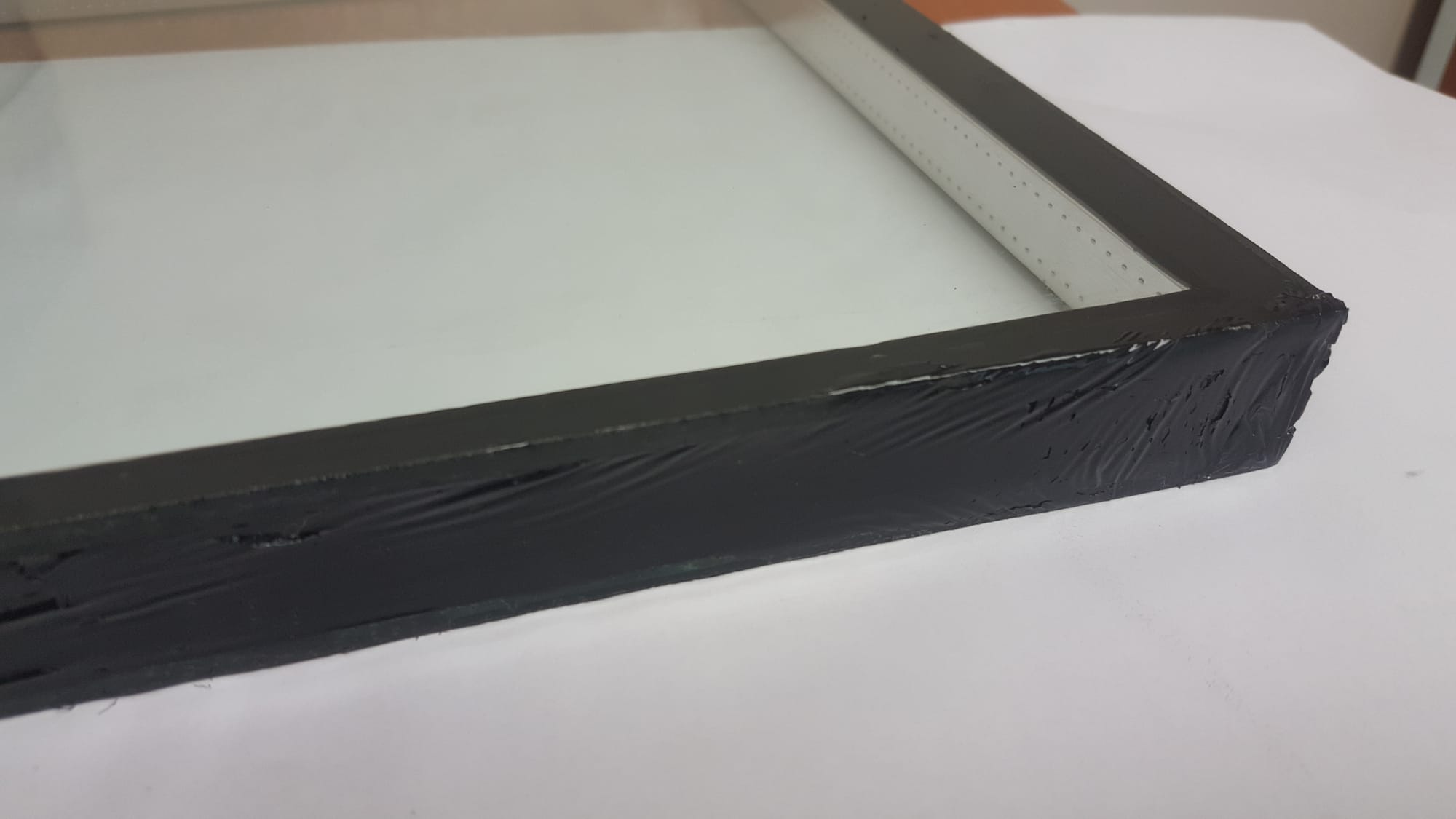